Murray
Corporation of America During World War Two
Detroit, MI
1913-1981
1913-1924 as the J.W. Murray
Mfg. Co.
1924-1927 as the Murray Body Corporation
1927-1981 as the Murray Corporation of America
This page added 3-22-2023.
In August 2013, I made a trip to the
Milwaukee Junction area of Detroit to visit the Ford Piquette Avenue
Plant Museum. It was at this plant that Henry Ford first produced
the Model T before moving production to the Highland Park plant.
When I was done, I noticed a large, multi-story factory to the north.
As I made my way towards this old factory, I wondered who's former auto
factory was. I was not able to determine this
information when I returned home after that trip. For almost ten
years, the ones and zeros that digitally represent the photos I took
that day waited on my computer hard drive to be able to turn into photos
on one of my webpages. In March 2023, almost ten years later,
while researching the Murray Corporation of America, I realized this
unknown factory I visited in 2013 was the former home of Murray, one of
the three big automotive body builders of the early automobile industry
in Detroit.
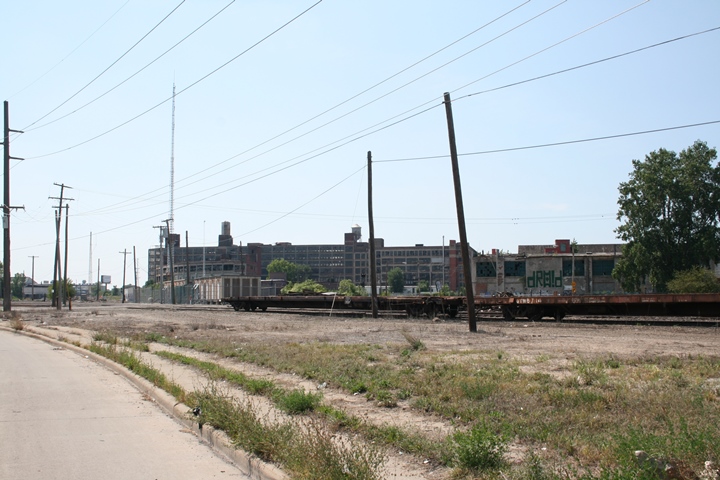
Milwaukee Junction got its name from the
former Milwaukee Railroad tracks that ran through the area. While
the area was quiet on the Sunday afternoon I was there in 2013, one
hundred years before the area was the center of much of Detroit's
growing automobile industry. Many auto companies were located in
the geographic area. Besides Ford and Murray, Anderson Electric
Car Company, Brush Motor Car Company, Cadillac, Dodge, Everitt-Metzger-Flanders,
Fisher Body, Hupp, Packard, Oakland, Studebaker, and Regal all had
factories at Milwaukee Junction. It is considered the cradle of
the Detroit auto industry.
This image is looking north across the former
Milwaukee Railroad tracks towards the former Murray Corporation of
America factory complex. Even from this distance, it can be seen
that this Albert Kahn-designed factory is huge.
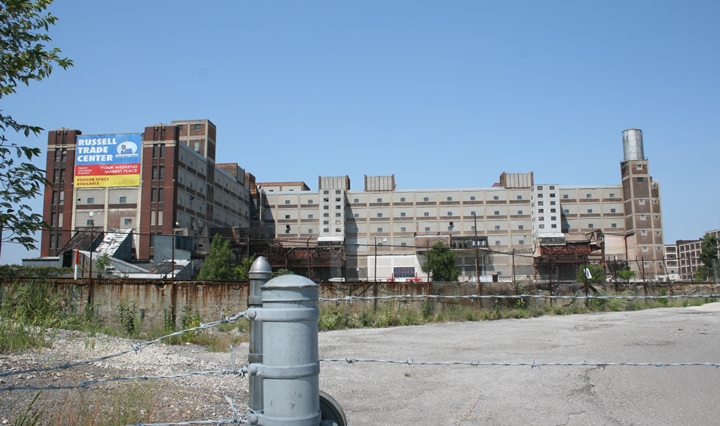
In 1915, Albert Kahn designed this seven
building 2,200,000 square foot complex for John William Murray, founder
and president of the Murray Corporation.
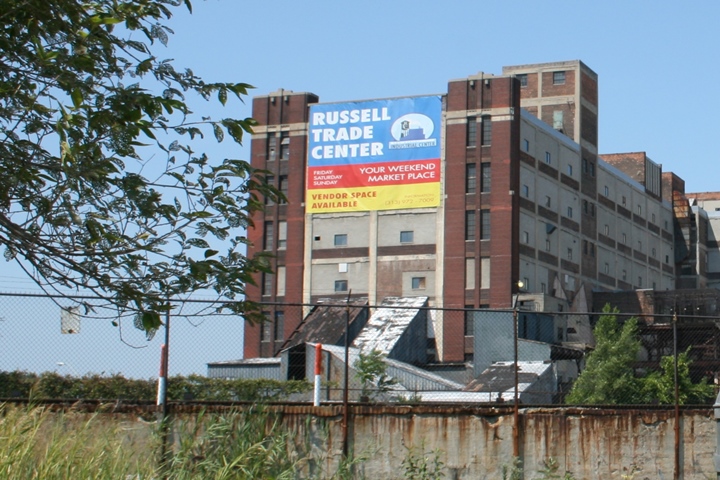
The two angled structures coming out of the
third floor of the south side of the west build appear to be the
location where the finished bodies exited the factory and were then
loaded on trailers to be transported to the company's various customers.
Currently, some of the over two million square feet in the complex are
part of the Russell Trade Center.
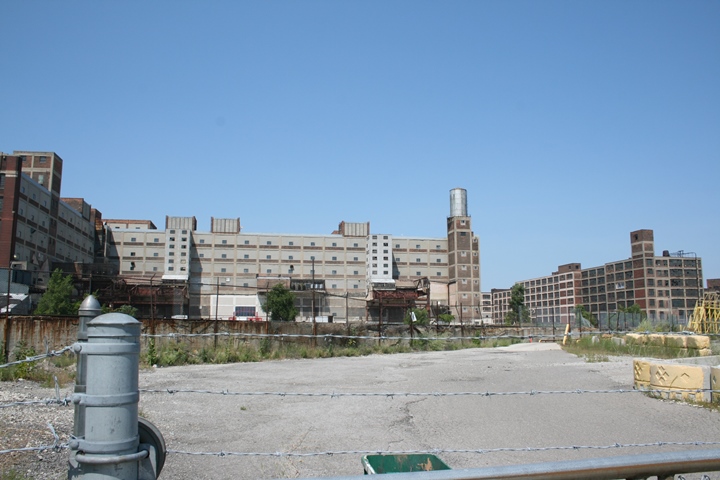
When it was designed and built, this was a
state-of-the-art factory. The Albert Kahn-designed factories in
Detroit all have an elegance not found in today's big box steel shell
factories.
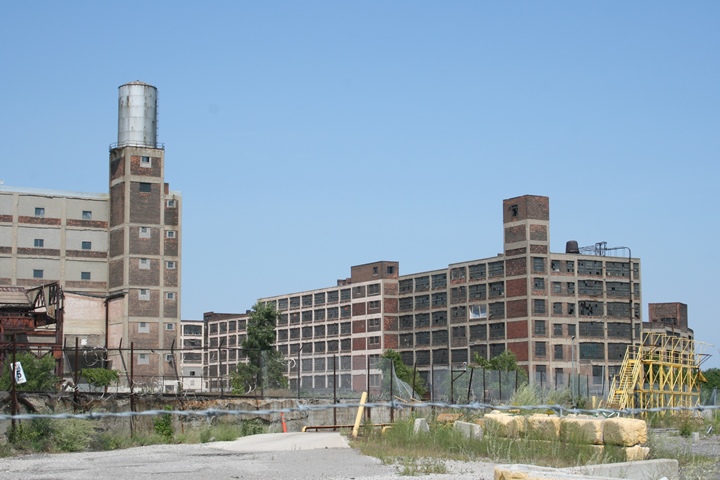
Even from this distance, it can be seen that
the buildings are in relatively good shape for being nearly one hundred
years old when these photos were taken.
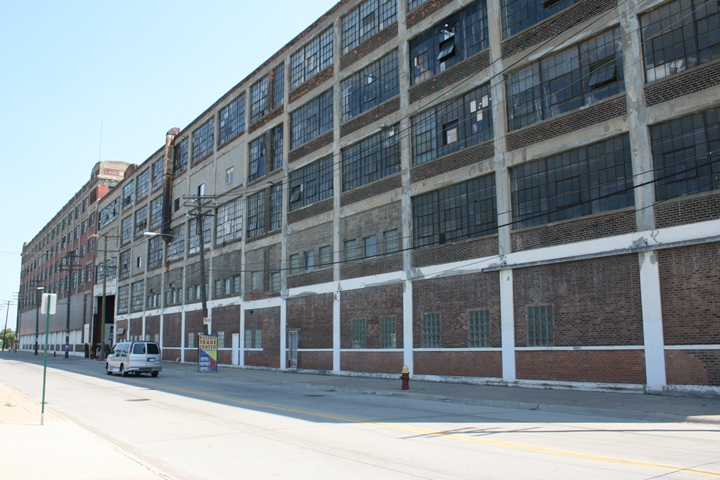
This image is on the north side of the
complex looking east on Clay Street. Again, it can be seen that
the buildings are in very good condition. While the former Packard
complex a mile to the south east of this area is more well known, it is
rather derelict. There are a lot of windows in the building.
Normally, when I visit an old factory like this, many of the windows are
broken out. This is not the case here. Any broken windows
have been repaired.
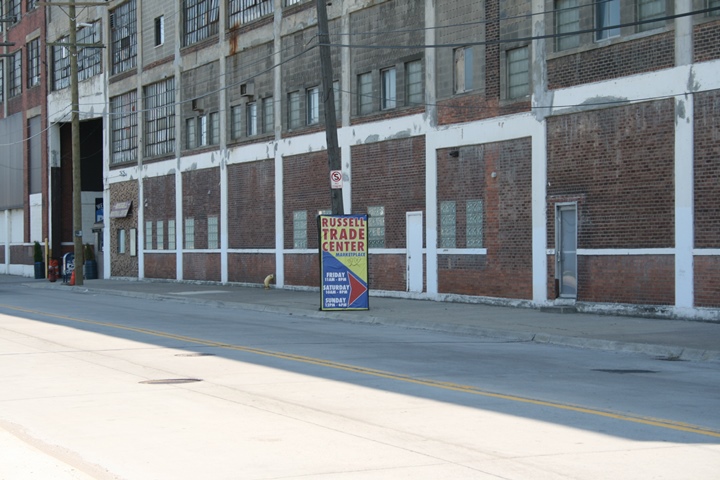
Just to the east of the power pole is an
entrance into the factory complex. I have seen this type of entrance
at other Albert Kahn factories in the Detroit area.
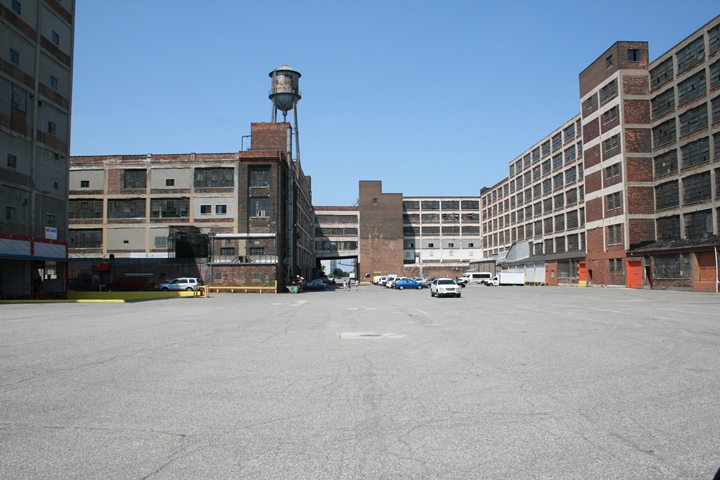
This image is looking north from inside the
courtyard of the complex. The area is well maintained.
Vehicles were parked at the north end of the courtyard and people were
visiting what shops located there.
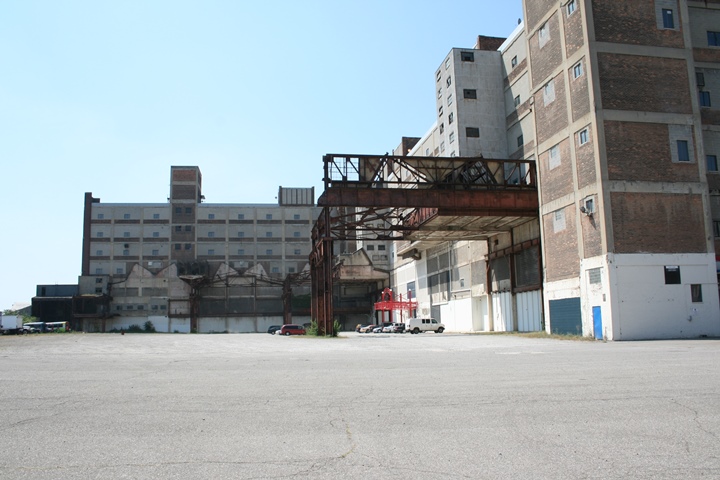
This image is looking to the west from the
south end of the courtyard. Notice how small the vehicles look
parked along the building compared to the size of buildings.
Unfortunately, Detroit is known for many of
the dilapidated and derelict buildings that once were proud factories
providing jobs and producing automobiles. The previously mentioned
former Packard plant is an unfortunate and well-known example. In
1960, the former Murray complex was purchased by Packard Properties and
re-named the Russell Industrial Center. Sixty different small
companies moved in and used most of the floor space. However, over
the years, ownership of the complex changed, most of the companies
moved out, and the Russell Industrial Center started to slide into
disrepair. However, Mr. Dennis Kefallinos purchased the complex in
the early 21st century and has spent the necessary money to restore some
of its original elegance.
In 1913, John William Murray and his son John
R. Murray formed the J.W. Murray Mfg. Co. whose main product was
providing steel stampings to the Detroit automobile manufacturers.
The company's products included fenders, hoods, cowls, and frames for
Ford, Hudson, Hupmobile, King, and Studebaker. In 1924, the J.W.
Murray Mfg. Co. merged with the C.R. Wilson Body Co., Towson Body Co.,
and the J.C. Widman Co. to form the Murray Body Corporation. The
C.R. Wilson Body Co. had a large customer base for its bodies that
included the Ford Motor Company. With the merger the new company
produced upwards of 70,000 bodies per year. Both of the original
Murrays left the company after the merger and new corporate inept
management sent the company into receivership in 1925. When the
company finally emerged from receivership in 1927, it was renamed the
Murray Corporation of America and had new management. The new
company continued to produce automotive bodies for various auto
companies until 1952. However, by then General Motors, Ford, and
Chrysler all had their in-house body making capacities, and Murray's
other customers slowly went out of business one by one. The company had
previously diversified into other products including plumbing and
household appliances. This portion of the company continued at
least through the early 1980s.
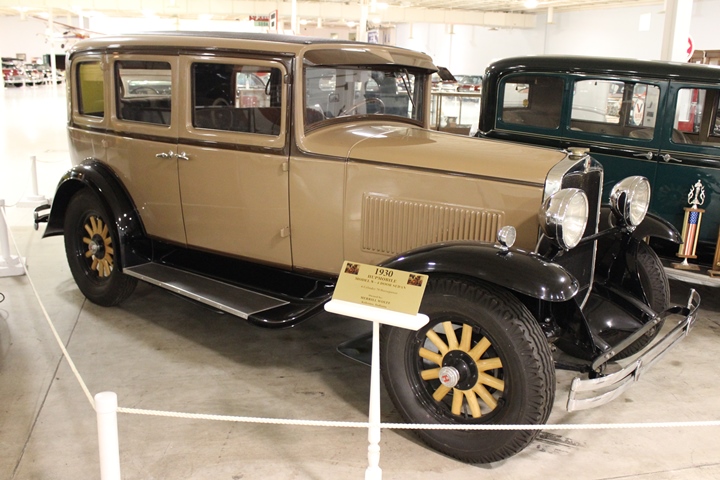
This 1930 Hupmobile has a Murray body.
Author's photo.
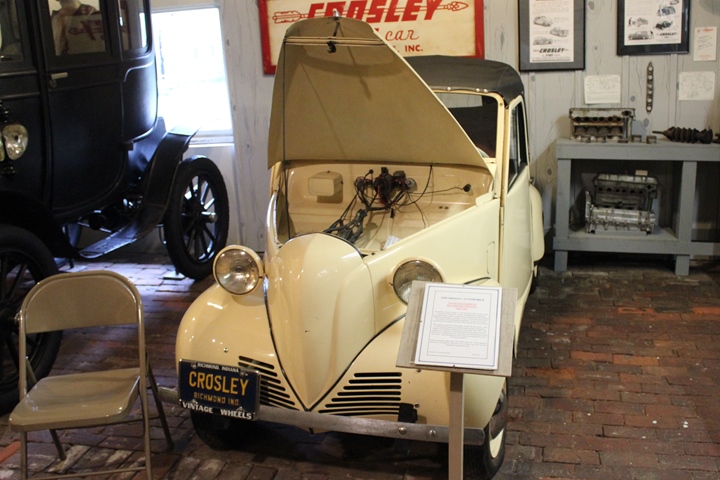
Crosley was another of Murray's costumers.
This 1939 Crosley has a Murray body. Author's photo.
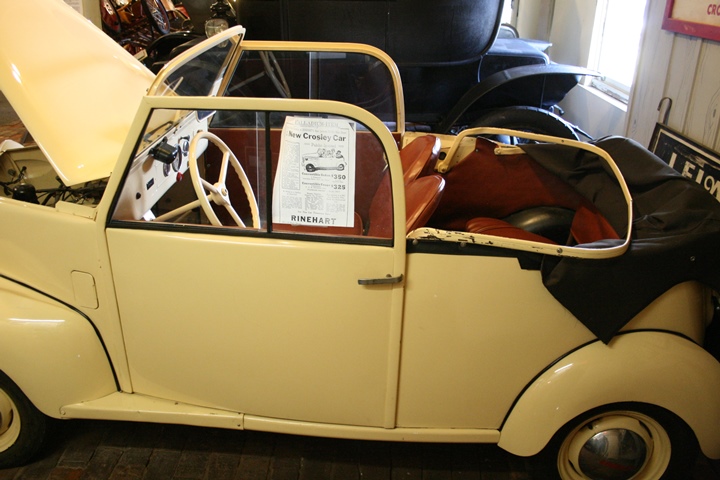
Author's photo.
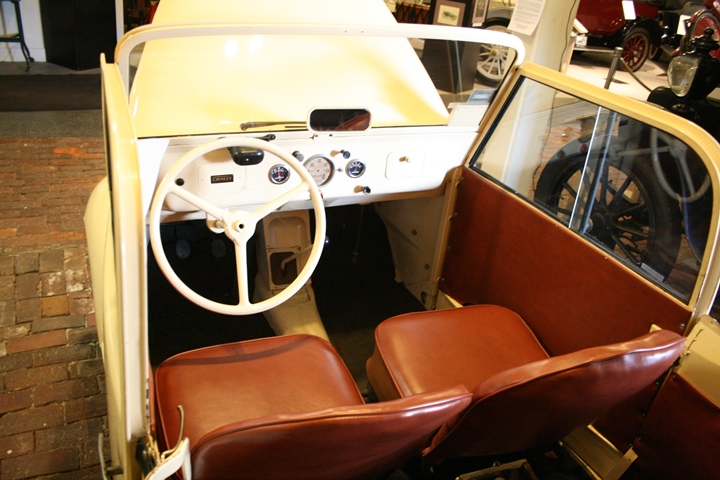
This view shows the interior of the
Crosley passenger cabin. Crosley went out of business in 1953.
Some of the last bodies Murray made were for Crosley. It had
finally run out of
customers. Author's photo.
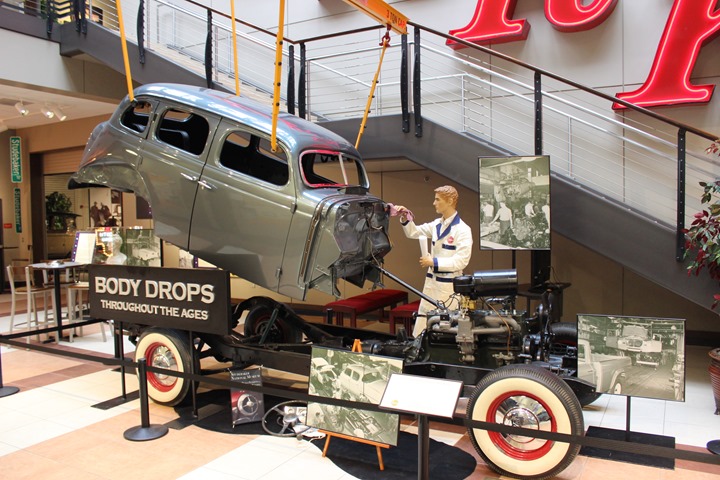
This former display at the Studebaker Museum
illustrates the body drop. The body manufacturers installed all of the
carpeting, seats, door hardware, and windows along with all of the
upholstery. Author's photo.
Murray Corporation of America World War Two
Products:
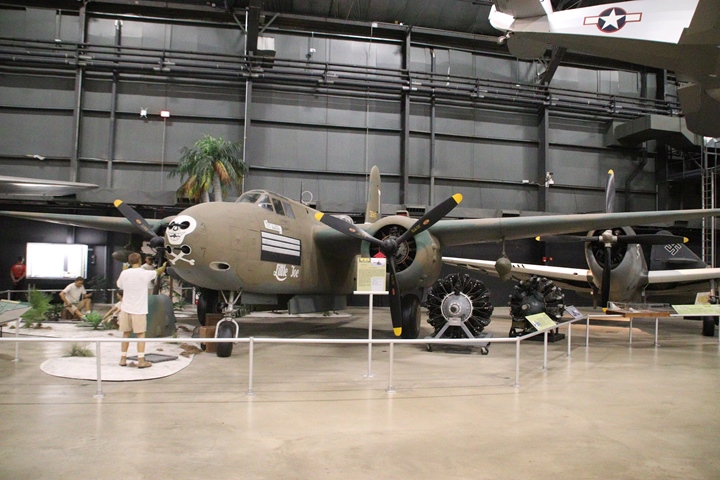
In January 1941, Murray accepted a
$26,000,000 contract from Douglas Aircraft for the manufacture of
A-20 inboard wings. Murray was the first company to utilize
automotive mass production techniques for the production of aircraft
parts. It used the same methods and presses for making aluminum
parts as it did for making steel auto bodies. Each A-20
inner wing section consisted of 5,400 parts and 55,000 rivets. The
contract was completed ahead of schedule in 1942. Author's photo.
In May 1941, the United States Army Air
Forces notified the Boeing Company that requirements for B-17s had
become larger than Boeing's ability to build them. This led to
the Douglas Aircraft Company and the Vega Division of Lockheed coming on
board as builders of the B-17 under license from Boeing. This was
during the same time period that the American aircraft industry was
going to Detroit to fabricate airframe components for many of the new
military aircraft being built. Because of the A-20 inner wing
project, Douglas chose Murray to build the outer wings, wings tips, and
engine nacelles for the B-17F model. As was typical of the era, it
took both Douglas and Murray a year to tool up and begin production.
During that period, Douglas added two new buildings for production of
the B-17 at its Long Beach, CA facility. The first Douglas B-17F
came off the Long Beach assembly line in late June 1942. For the
next year, Murray delivered 605 B-17 outer wings and wing tip sets to
Douglas. It also produced 2,420 engine nacelles. With the
introduction of the B-17G model at Douglas in June 1943, Murray's contract
was not renewed. For whatever reason, this contract went to
Murray's chief competitor, Briggs.
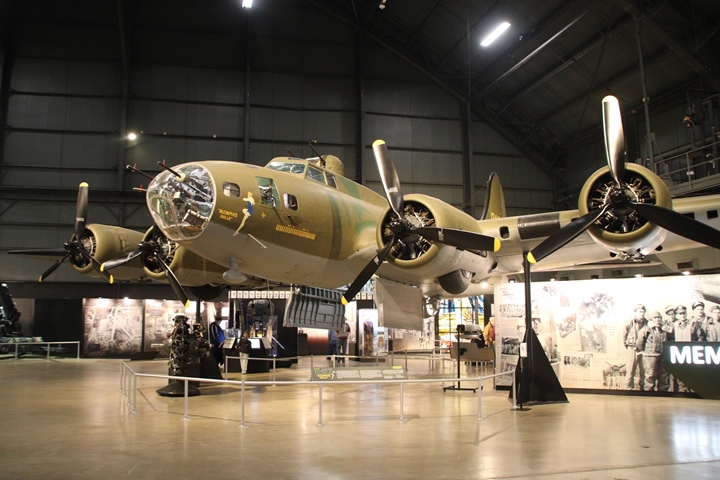
This is the B-17F "Memphis Belle" at the
National Museum of the United States Air Force in Riverside, OH.
The "Memphis Belle" was built by Boeing but is identical to the ones
Douglas made. Author's photo.
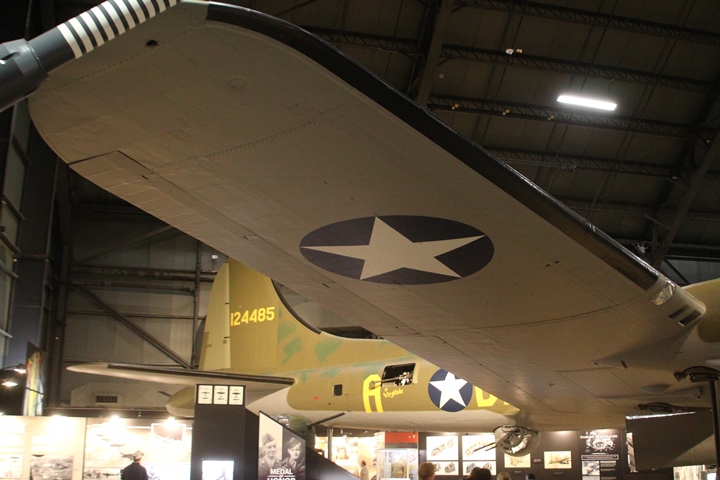
There are two seams in the wing that
separate the outer wing from the wing center section and the wing tip.
One can be seen next to the landing light and the other out towards the
tip of the wing. Author's photo.
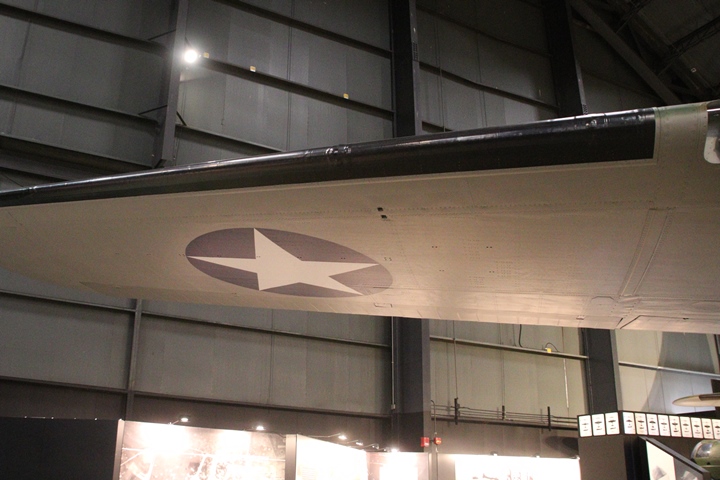
The seam where the outer wing joins the center
section can be seen in the right side of the photo. Author's photo.
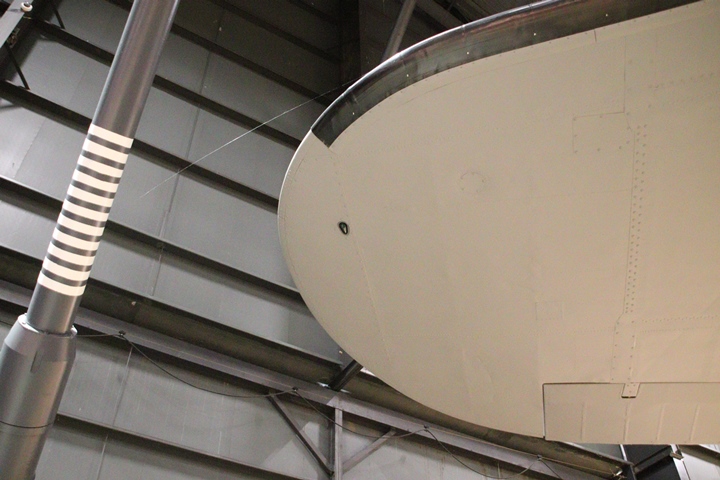
This shows the seam between the outer wing
and the wing tip. Murray produced both components for the
Douglas-built B-17F. Author's photo.
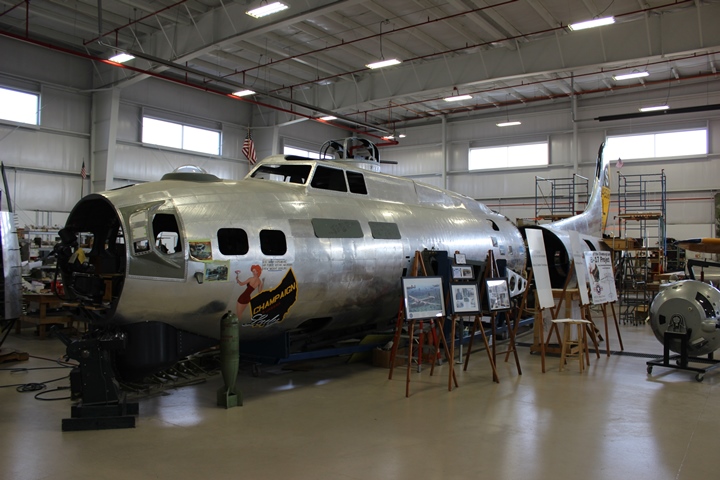
This Vega-built B-17G "Champaign Lady" is undergoing total restoration
at the Champaign Aviation Museum in Urbana, OH. Author's photo.
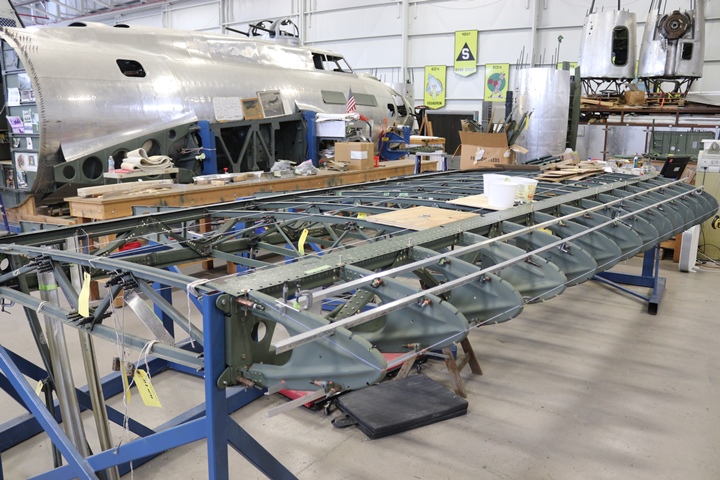
The wings for the "Champaign Lady" are being
built from scratch by museum volunteers. This view of one of the
outer wing sections shows the details of the construction. Author's photo.
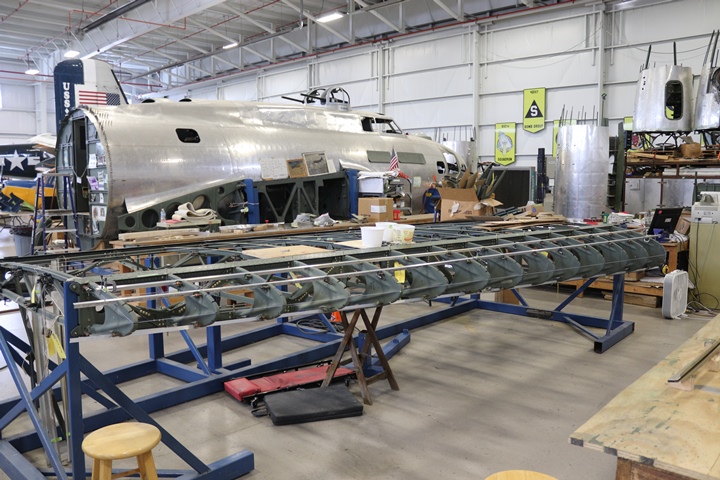
Author's photo.
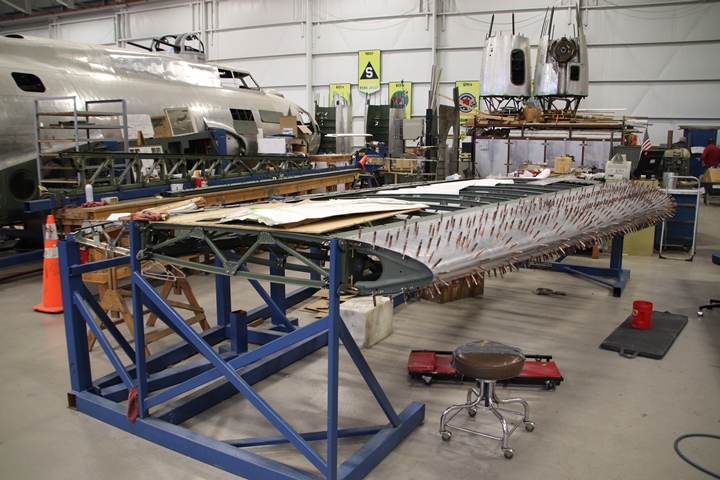
This and the next two images were taken at a
later date. Author's photo.
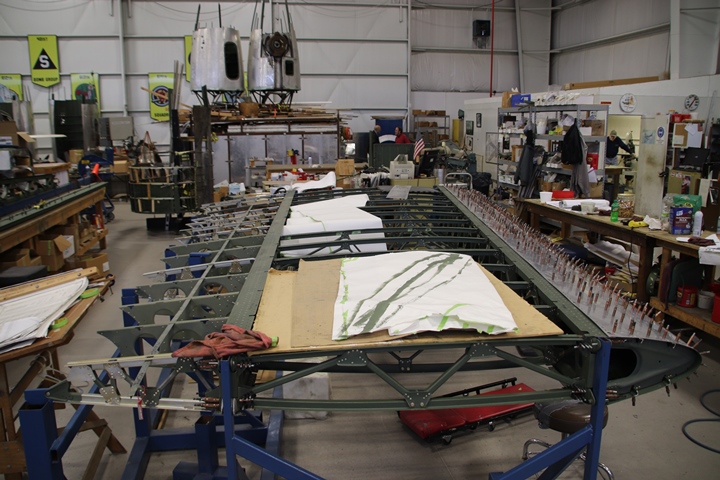
Author's photo.
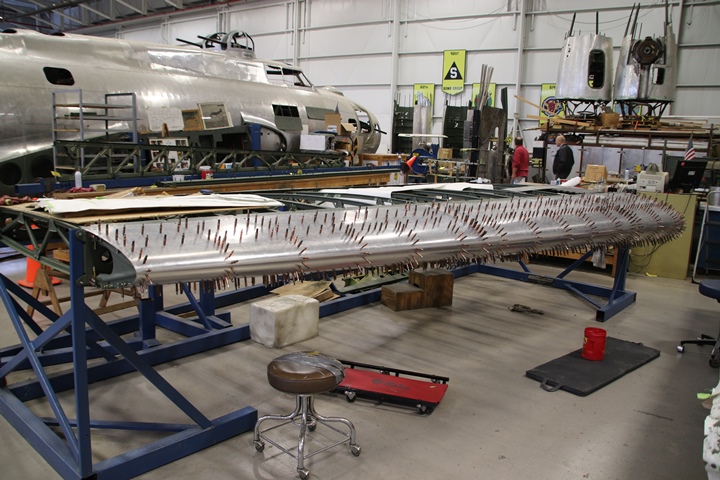
Author's photo.

This B-17 engine nacelle shows the
construction of the unit. Author's photo.
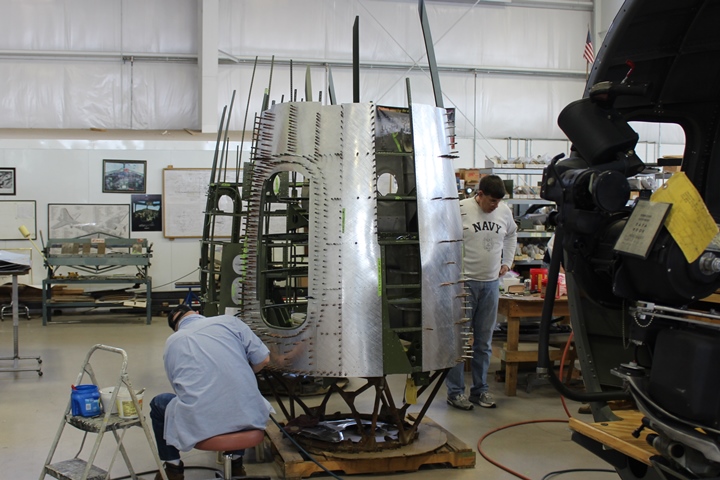
Author's photo.
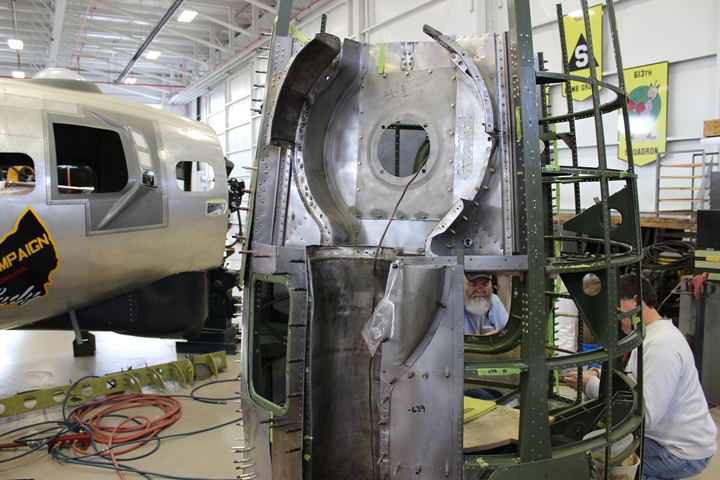
Each engine had a General Electric turbo
supercharger to allow it to fly at high altitude. This image shows
the location of the unit in the bottom of the nacelle. Author's photo.
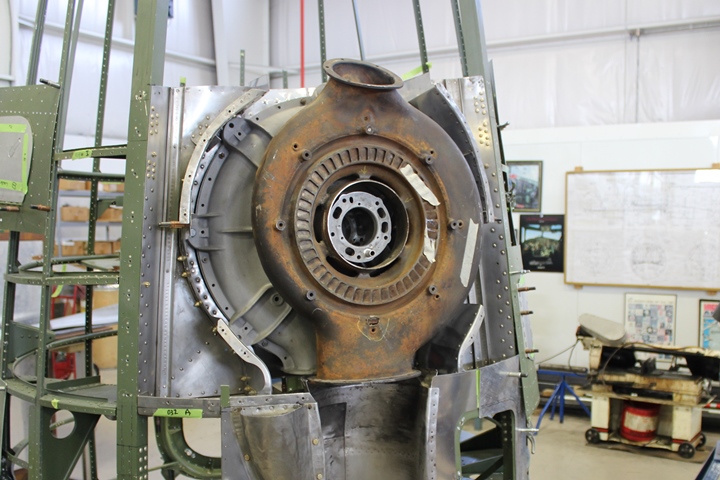
A partially assembled turbo supercharger has
been installed, showing how it fits into the nacelle. Author's photo.
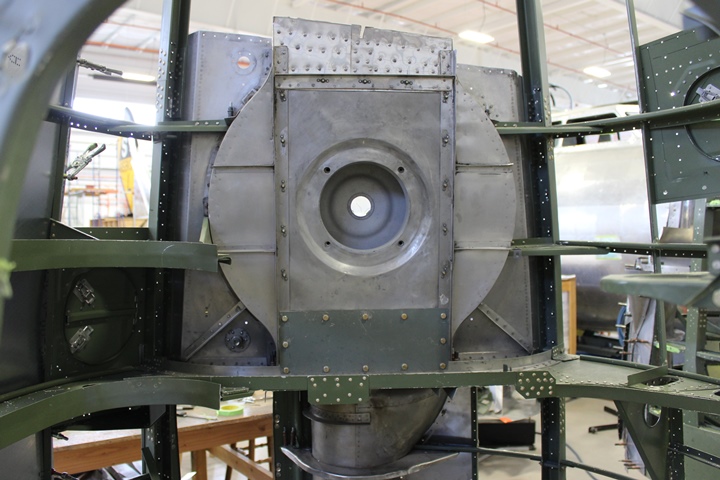
This is an interior view of the engine
nacelle. Author's photo.
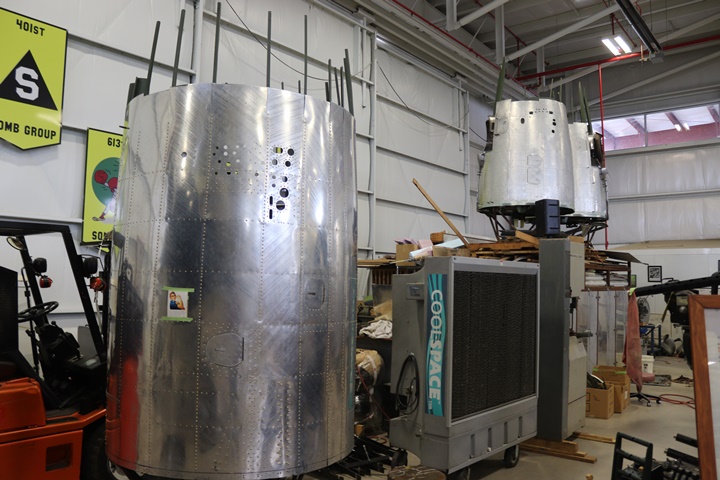
This image shows three nacelles awaiting
installation. Once the wings are completed, the nacelles can be
installed on them. Author's photo.
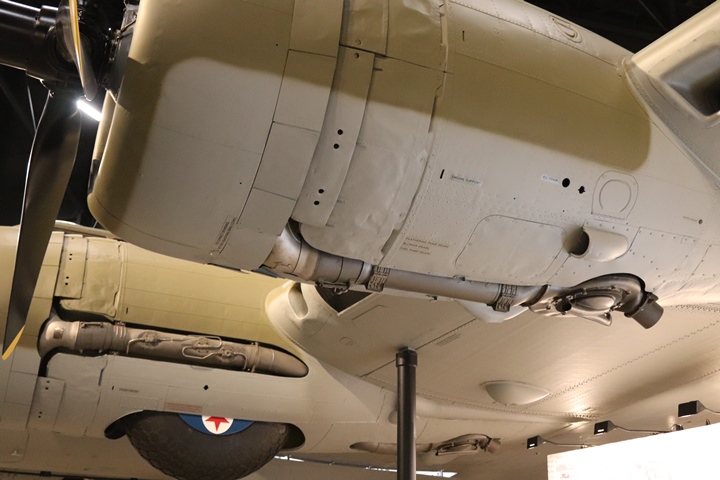
This image shows two the port side engine
nacelles on the "Memphis Belle." Author's photo.
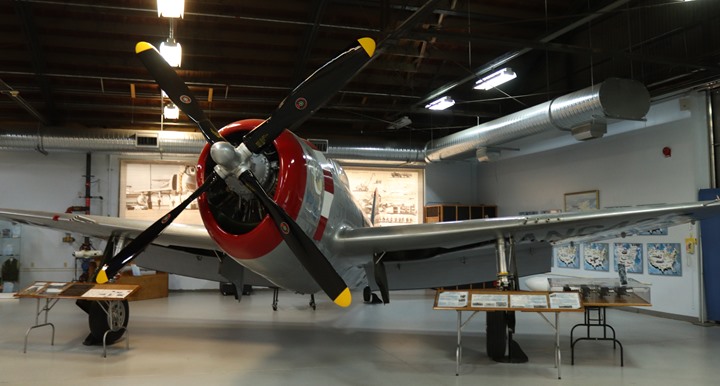
Next, Murray began the production of wings for the Republic P-47G
Thunderbolt. This was the Curtiss-Wright Corporation's
license-built version of the P-47. Only 354 were built.
Author's photo.
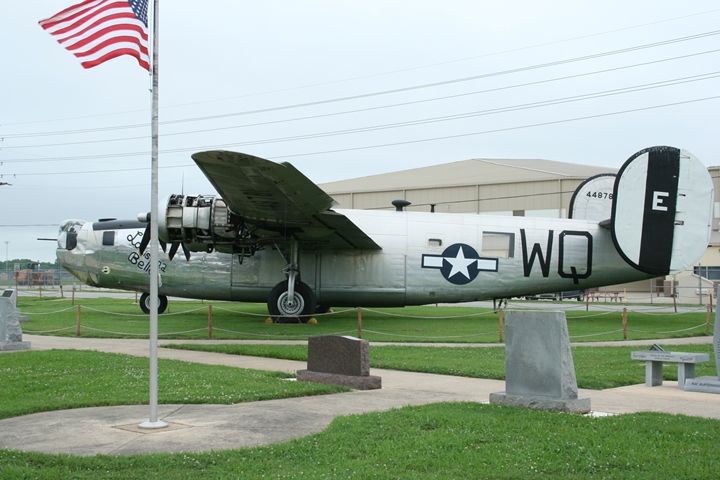
This Ford-built B-24J is on display at the Barksdale Global Power Museum at Barksdale AFB in Bossier City,
LA. Murray produced an unknown quantity of various subcomponents
for the 6,792 B-24s that Ford at the aircraft assembly plant in nearby
Willow Run, MI. Ford also made 955 knock-down B-24s that were
assembled by Douglas in Tulsa, OK and 939 knock-downs that were
assembled at the Consolidated plant in Fort Worth, TX. Ford also
made enough spare parts to make another 452 aircraft. There was
plenty of opportunity for Murray to use its stamping facilities and
workforce to fabricate sheet metal parts and then assemble into
subassemblies for the Ford-built B-24s. Many of these components
were stainless steel stampings.
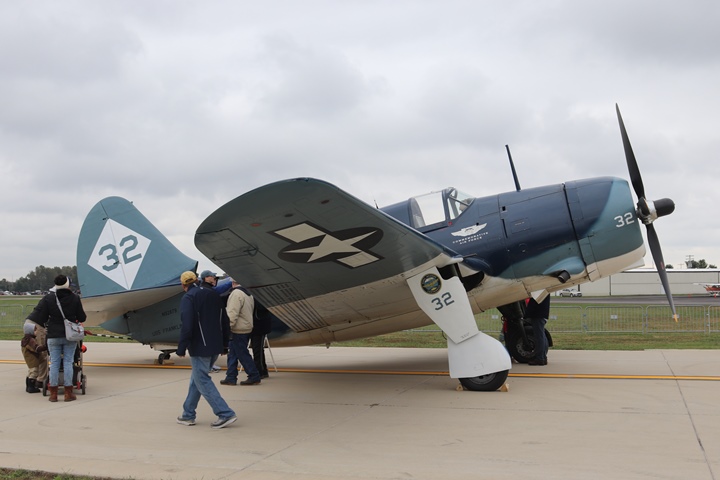
Murray was also contracted by Curtiss-Wright
for the manufacture of rudders for the SB2C dive bomber. The SB2Cs
were assembled by Curtiss in Columbus, OH. Author's photo.
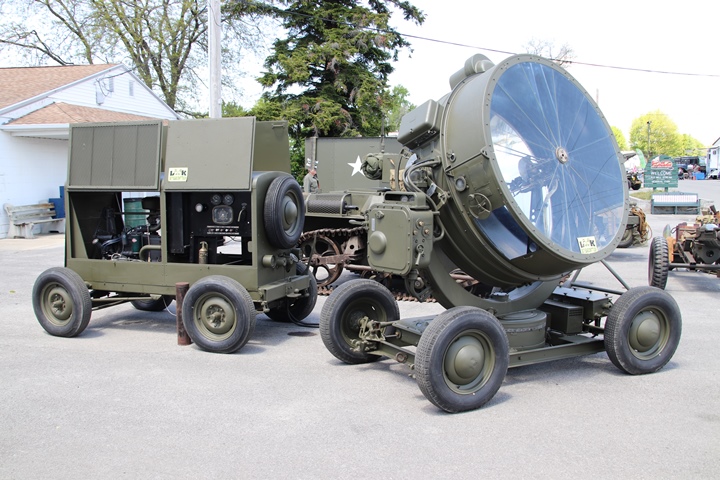
Murray also made steel stampings for
anti-aircraft search lights. It substituted steel stampings for
the replacement of aluminum castings which saved 100,000 lb. of aluminum per month. There were two different companies that made search
lights during World War Two. One was made by General Electric as
shown above. It is unknown for which company Murray made the
search light parts for. Author's photo.
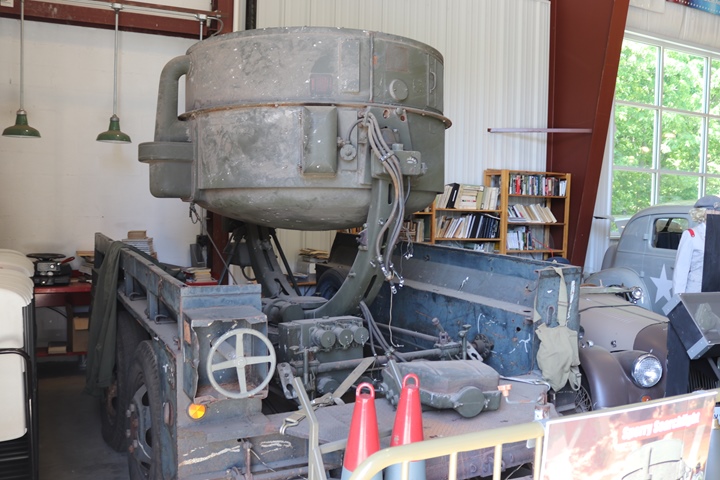
The Sperry Gyroscope Company built
search lights like the one shown here. Author's photo.
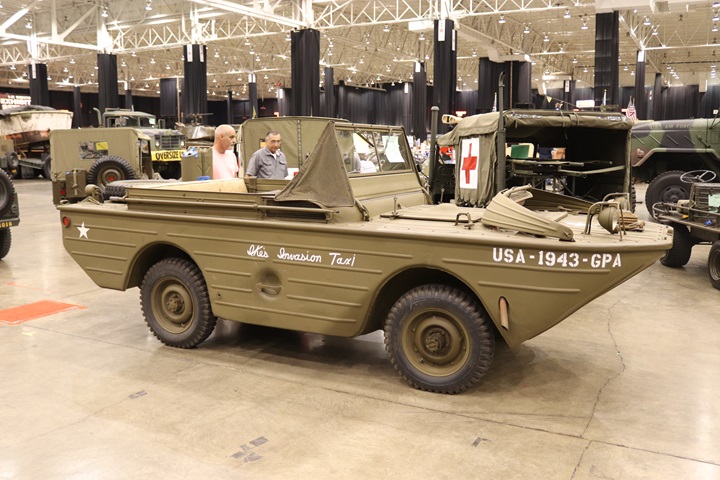
The Ford Motor Company produced 12,782
amphibious jeeps during World War Two. Murray produced the frames
for these vehicles. Author's photo.
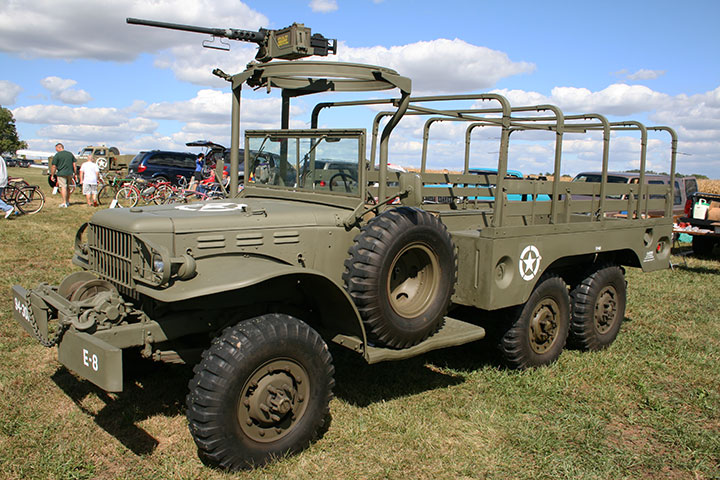
Dodge built 43,224 WC-62/WC-63 Dodge 6x6 1-1/2 ton
trucks at its Mounds Road Plant in Warren, MI. Murray Company
officials noted that Murray also made frames or frame parts for this
truck. Author's photo.
Murray also had $4,676,000 in major contracts
during World War Two.
Table 1 - Murray Corporation of
America's
Major World War Two Contracts
The information below
comes from the "Alphabetical Listing of Major War Supply
Contracts, June 1940 through September 1945." This was
published by the Civilian Production Administration, Industrial
Statistics Division. Table added 2-5-2023. |
Product - Customer |
Contract Amount |
Contract Awarded
Date |
Completion
Date |
Burlap Jute -
Army Corps of Engineers |
$354,000 |
1-1942 |
1-1942 |
Gun Parts - Army Ordnance |
$400,000 |
4-1942 |
9-1942 |
Flash Hiders
M1923 - Army Ordnance |
$83,000 |
12-1943 |
5-1944 |
Cartridge
Cases M13 - Army Ordnance |
$3,839,000 |
5-1944 |
1-1946 |
Total
|
$4,676,000 |
|
|
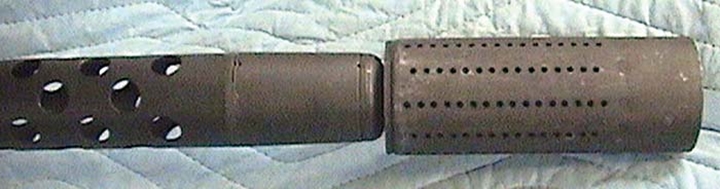
This image shows an M1923 flash hider on
the end of a .30 caliber machine gun barrel. Murray redesigned
the M1923 to utilize stampings instead of the part being a machined
part. This was as more cost effective design.
Murray Corporation of America World War Two
Scranton, PA Plant: In early 1944 Murray was designated to begin
building B-29 outer wing sections. While the company had floor
space at its plant in Detroit, there was a critical labor shortage in
the area. This was not the case in Scranton, PA, so Murray built a
government owned factory in Scranton, PA for production of B-29 outer
wings. During 1944, the company had use of a local armory to train
employees so they would be prepared to start the manufacture of wings in
early 1945 when the plant opened. After World War Two Murray
purchased the plant and produced gas and electric stoves, sinks, and
bathtubs.
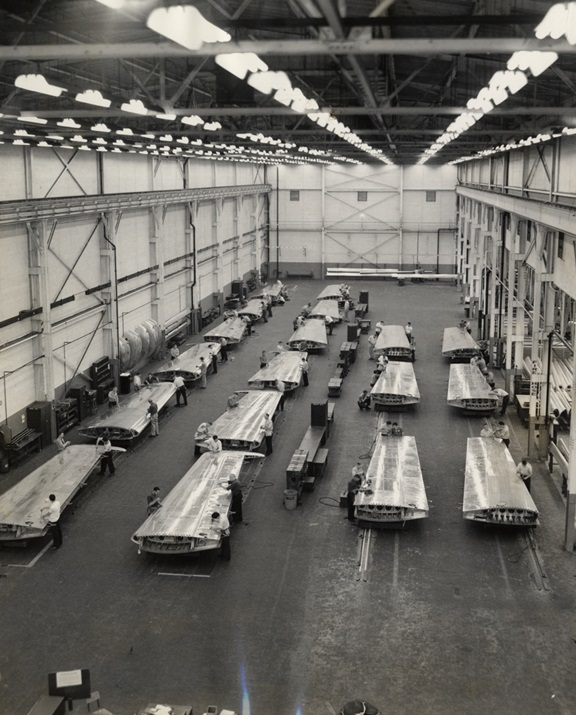
This image courtesy of the Detroit Public
Library National Automotive History Collection shows final
assembly of B-29 outer wing sections at Murray's Scranton plant.

This Google Maps satellite view shows the
plant as of today.
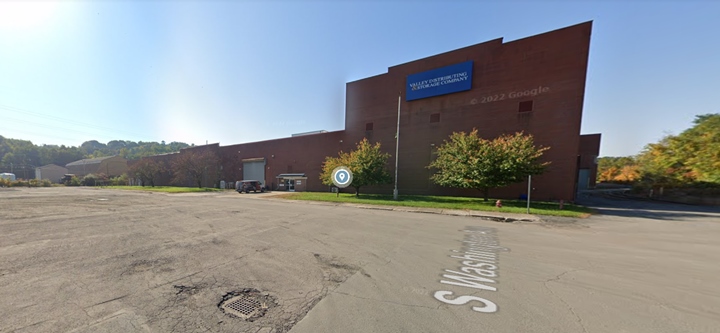
This is the Google Maps street view looking
to the south from the end of South Washington Street.
One last look at the Murray plant in
Detroit, MI.:
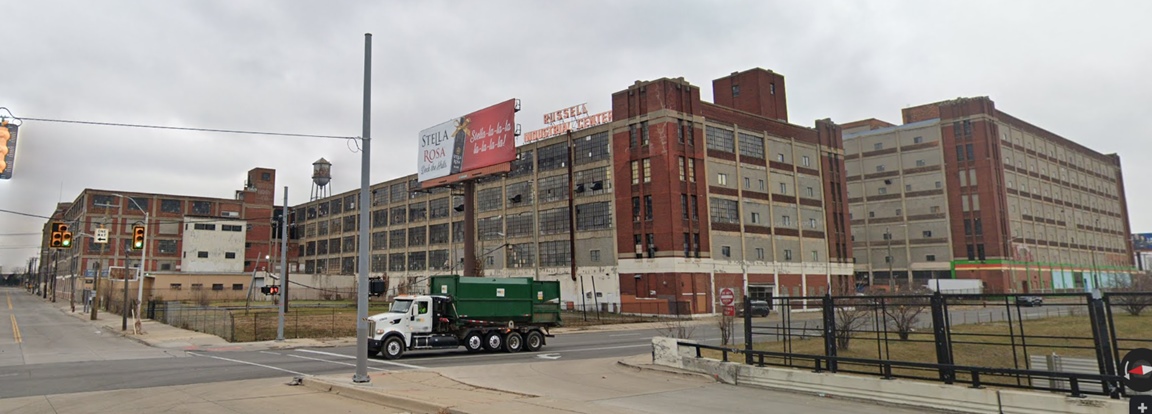
This Google Maps street view shows the
massive elegance of the Murray plant in Detroit.
|